Swedish innovation leads the way in wind turbine blade recycling
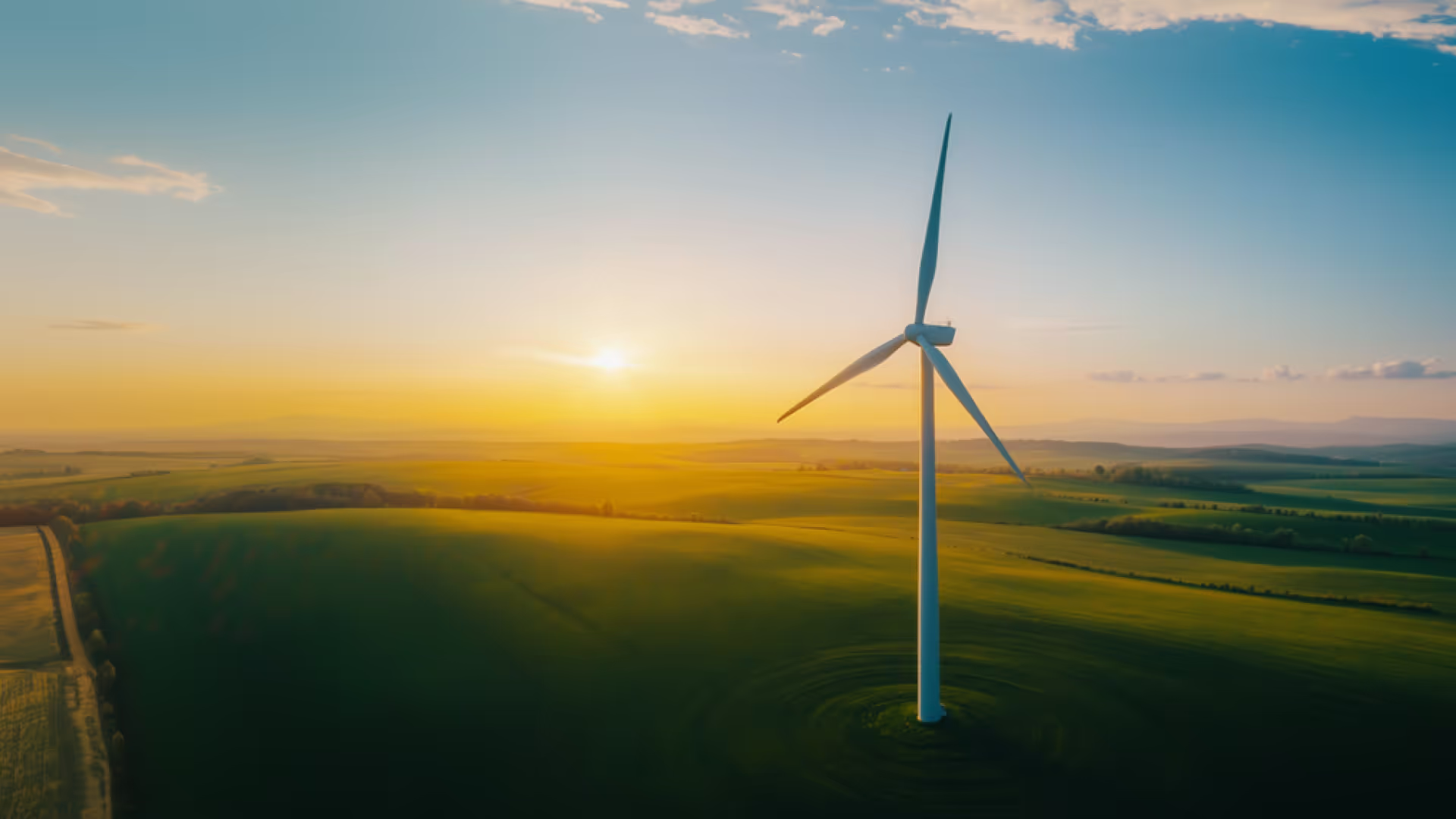
As global wind capacity rises to new heights, the sustainability of green energy faces a significant bottleneck – recycling of the turbine blades that drive this renewable force.
Wind turbines supplied 19% of all the EU’s electricity in 2023. After a 25-year lifespan, turbine blades, which are 10–15% of the mass and hard to recycle, are as of now, a wasted resource, pun intended.
As we move closer to the first generation of turbines reaching their end of life, there is an urgent call to action to offer sustainable solutions upon decommissioning. Effective solutions require collaborative efforts, not only among companies but also from customers who might benefit from the reclaimed materials. And there is hope.
A Swedish collaboration involving Librixer, Skellefteå Kraft, AfterWind, and The Swedish Wind Energy Association adds to the potential solutions by introducing a dry, energy-efficient recycling process. AfterWind financed the wind turbine blade recycling test, Skellefteå Kraft supplied segments of decommissioned blades, and the Swedish Wind Energy Association acted as a facilitator. The collaboration represents an important step towards responsible material management.
Librixer, a greentech company with the aim to improve industrial recycling, conducted the test.
Librixer successfully liberated the components of the dismantled wind turbine blade using their Librixer Liberator machine, which employs a unique comminution technology process to liberate materials effectively. Fibers emerged, largely separated from the epoxy, which turned into dust, along with the remaining materials such as balsa wood, foam, and phenolic resin. Once freed, the materials can be sorted and recycled individually.
Hanna Karlsson, project manager and nanotechnology engineer at Librixer, comments,
“Our technology supports the recycling of wind turbine blades through a mechanical, energy-efficient process. This test marks an important step toward achieving industry circularity.”
Future initiatives include testing various blade types and composites to understand the potential for reuse, reducing environmental impact, and realizing a sustainable wind energy ecosystem.
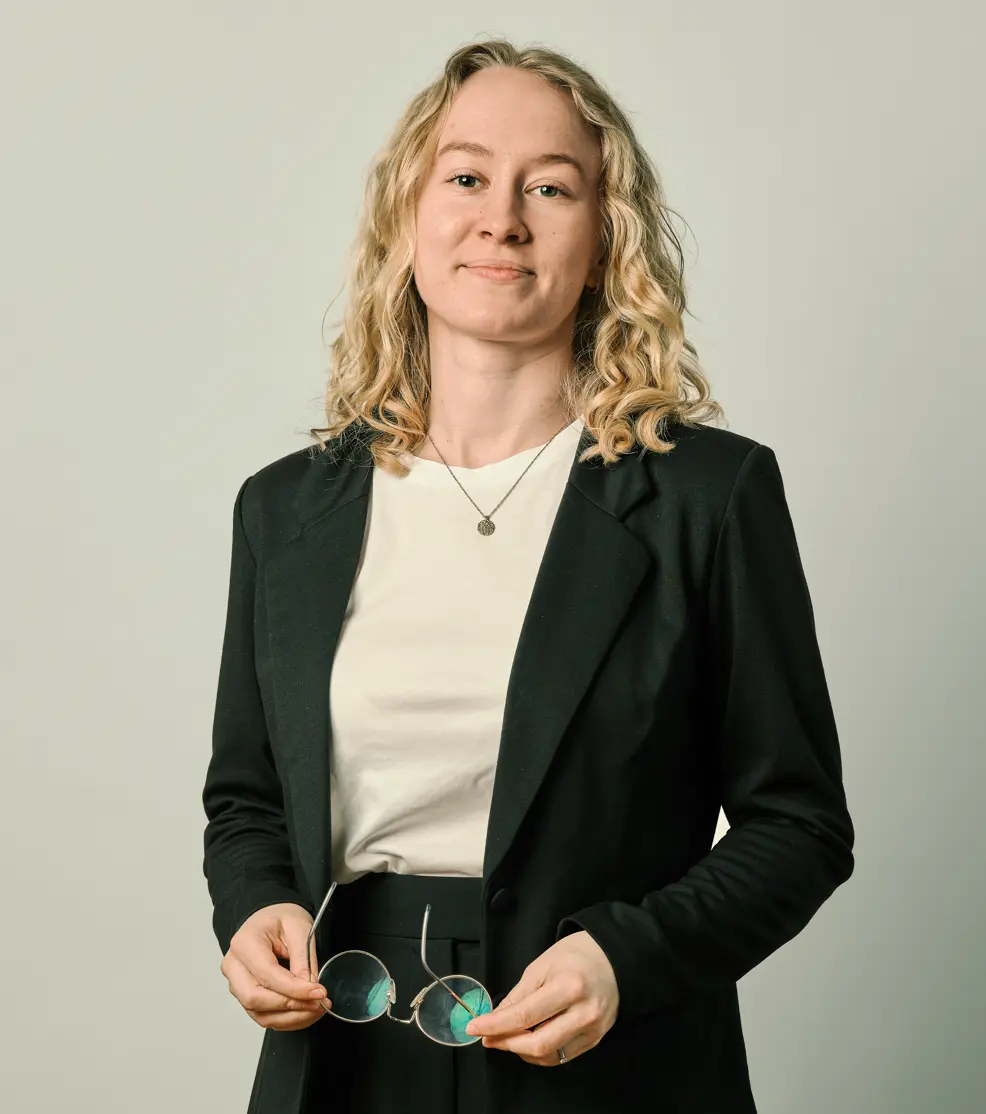
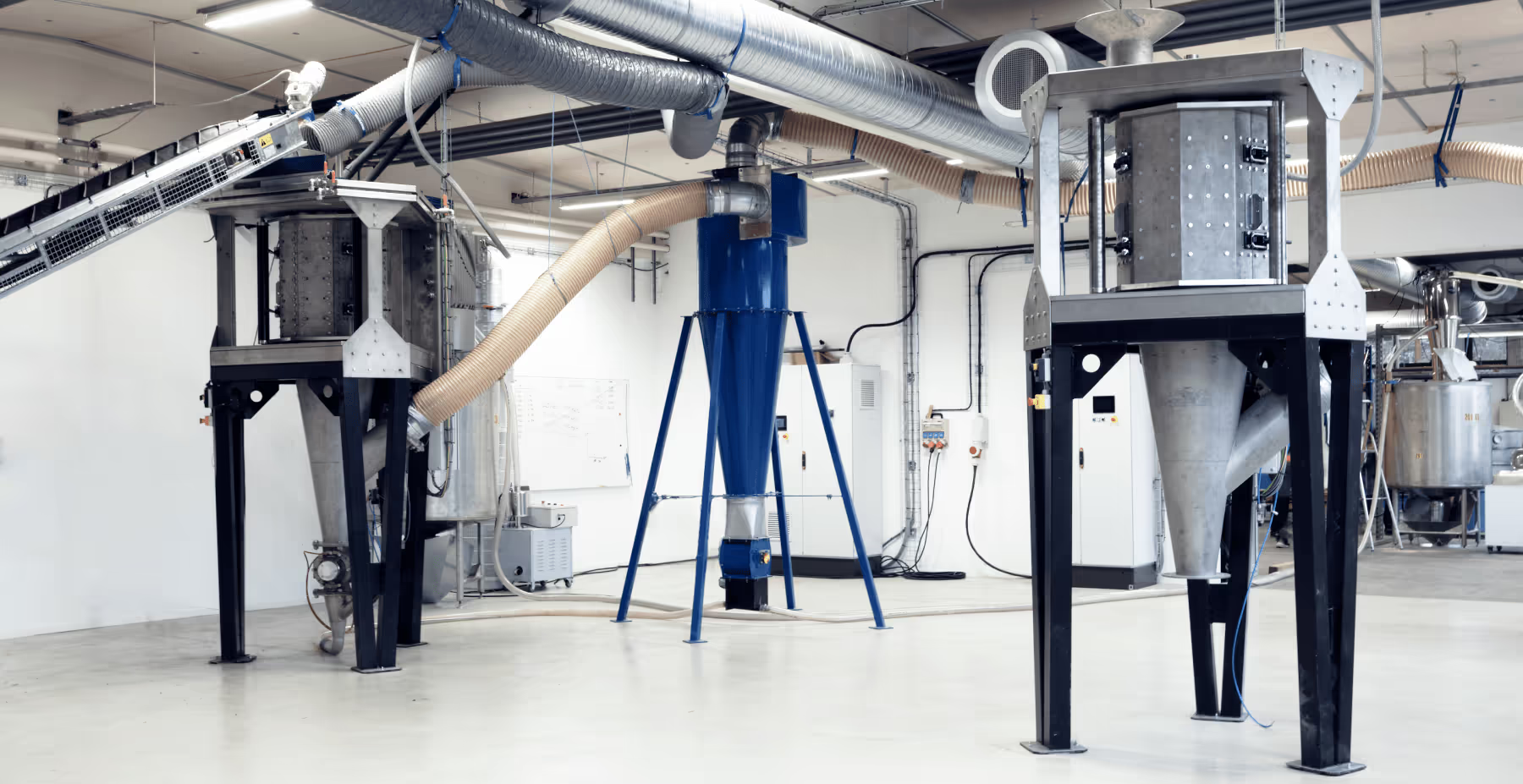
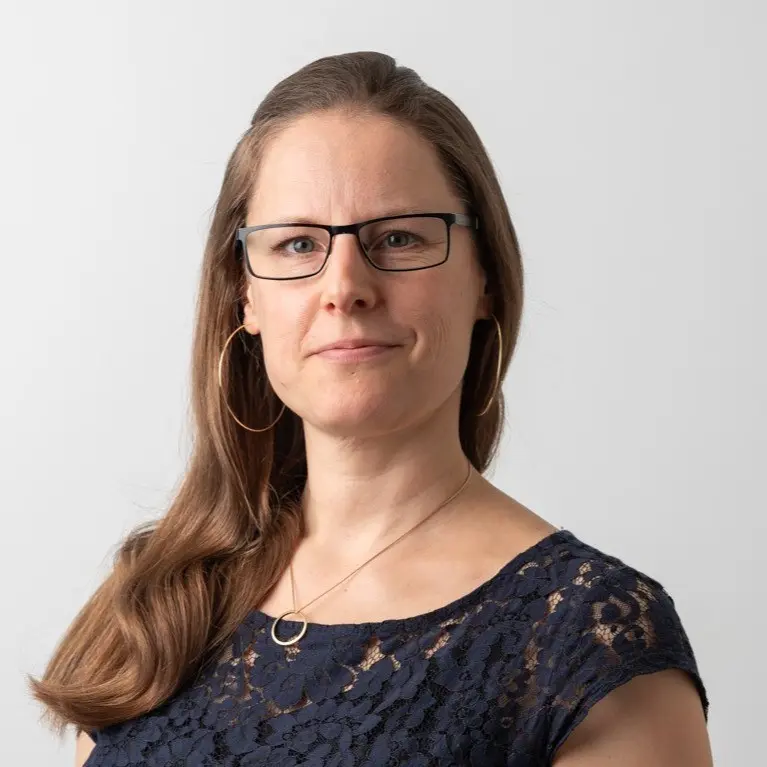
“The wind power industry is fully committed to finding market-based solutions for the sustainable management of wind turbine blades made from fiberglass composites. It’s a challenge shared with other industries, such as the boat industry, and we must all put our heads together. That’s why it’s very exciting to collaborate with Librixer to test how their technology can be used for this purpose, and we are eager to see the results.”
– says Ylva Tengblad, Sustainability Manager at the Swedish Wind Energy Association
There are other recycling methods for wind turbine blades, such as chemical, thermal, and mechanical. Each method comes with its own pros and cons and can face limitations regarding energy usage and environmental impact. Chemical recycling consumes a significant amount of energy (21–90 MJ/kg) and relies on harsh chemicals. Thermal methods like pyrolysis use moderate energy (24–30 MJ/kg) but can weaken fibres, reducing their reuse value, while also creating air pollution. Current mechanical recycling is less energy-intensive (0.1–4.8 MJ/kg) but can damage the fibres to a degree that restricts their application to low-end uses.
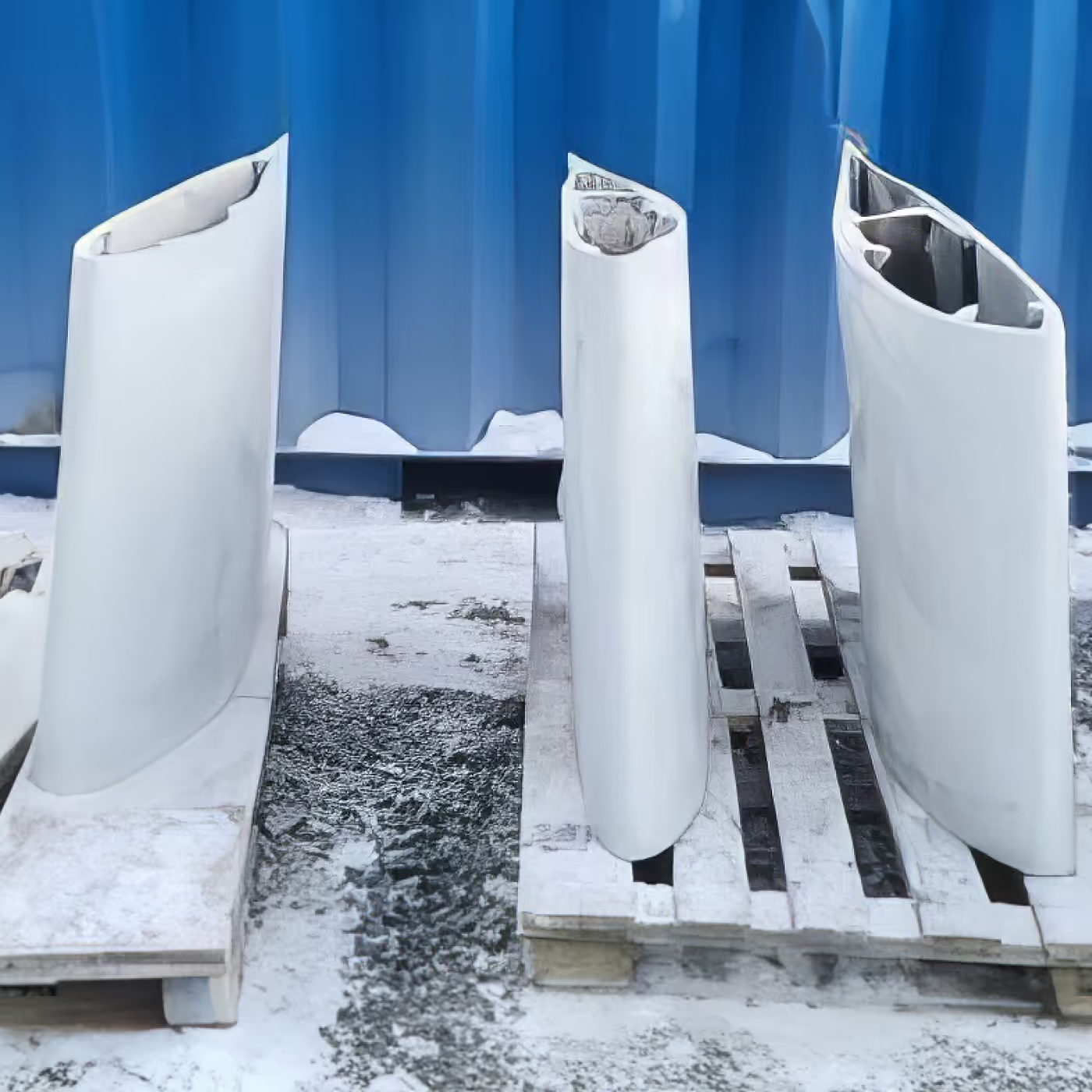
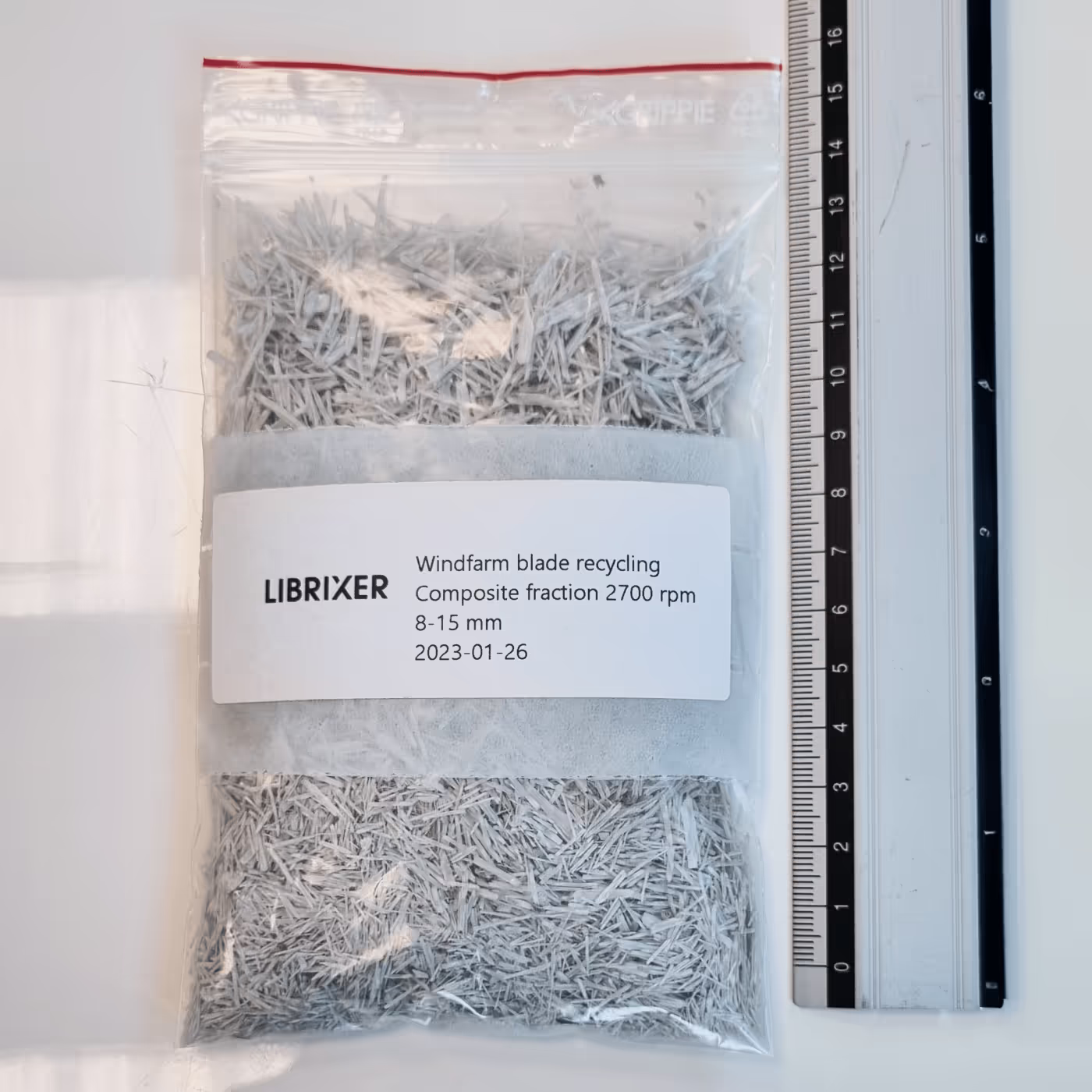
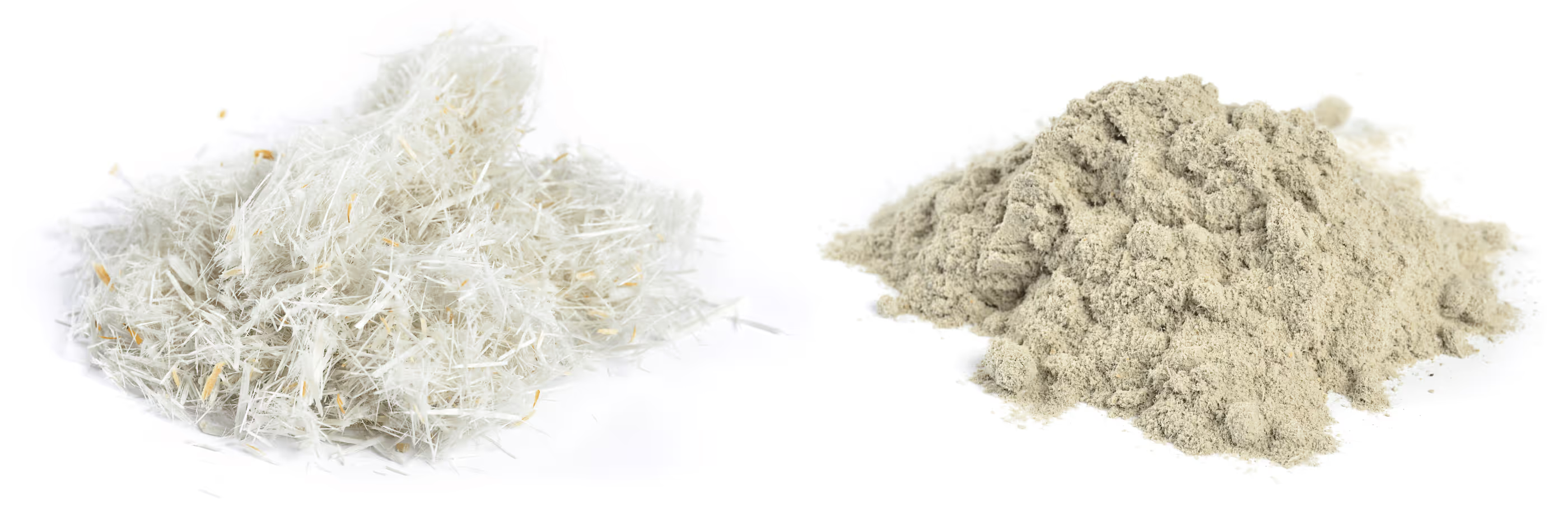
Librixer offers a mechanical, dry recycling technology that conserves the quality of fibres with relatively low energy consumption, thus addressing the drawbacks of other methods. The Liberator machines disassemble turbine blades into component materials—such as glass and carbon fibres, epoxy, balsa wood, and foam – without harsh chemicals or high-impact processes that compromise material integrity. This method allows for the materials to be sorted and repurposed while maintaining their original quality, promoting a circular economy for turbine blades. The process’s energy efficiency and cleanliness significantly enhance its sustainability and market potential.
Sebastian Vinterek from Skellefteå Kraft mentions,
“This work mirrors our commitment to environmental sustainability through innovative end-of-life management for turbine components.”
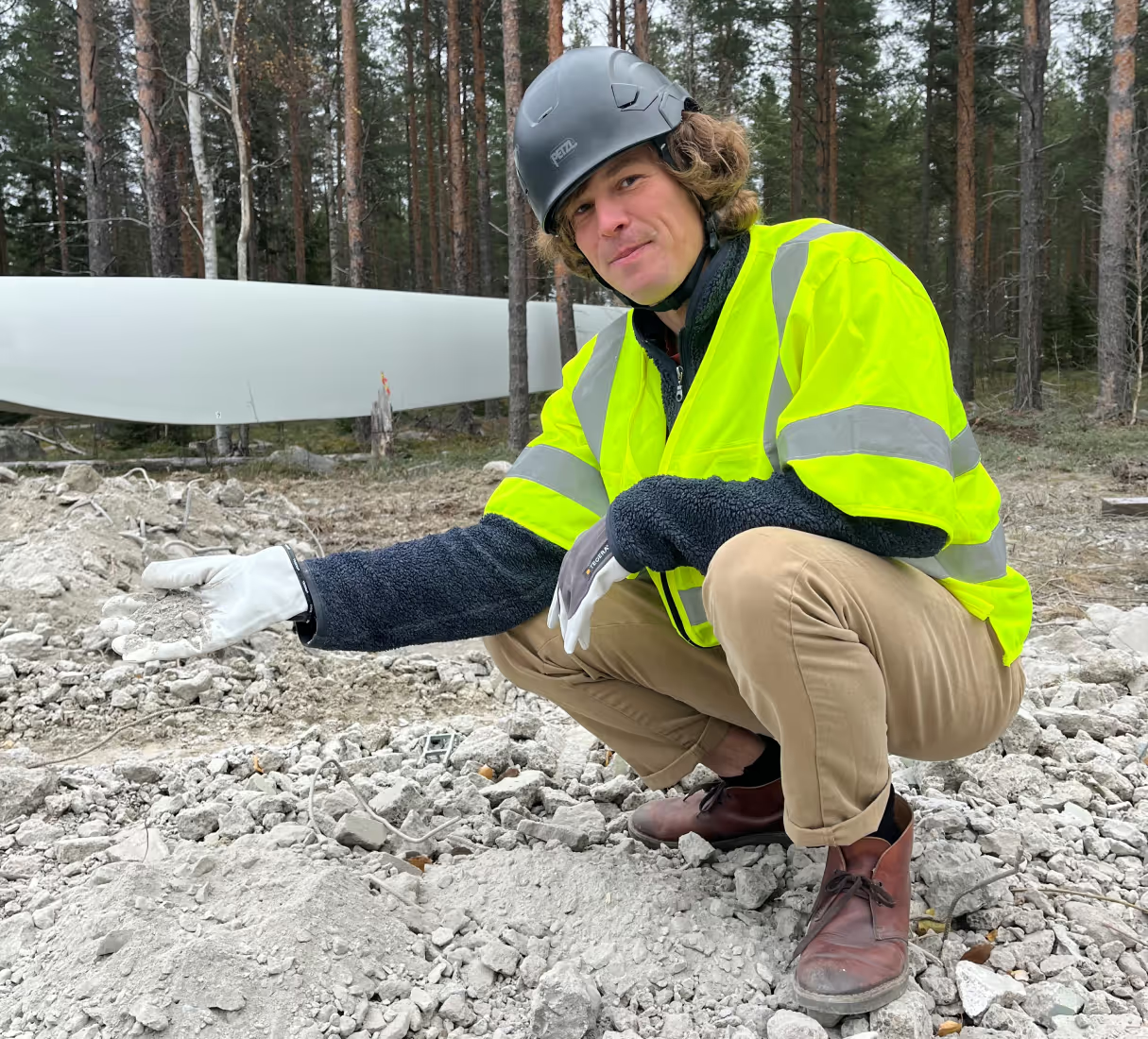
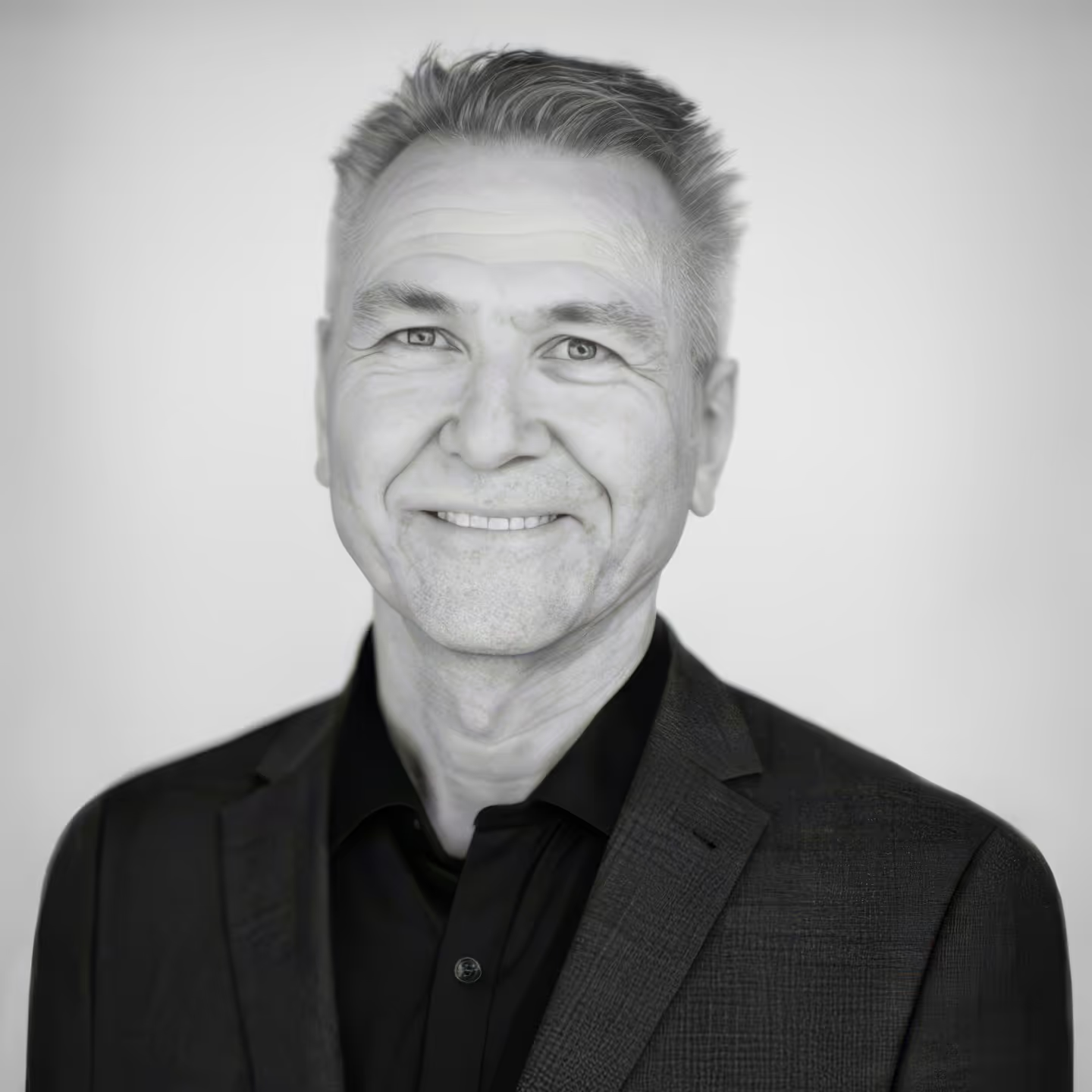
Henrik Selstam, CTO at AfterWind, acknowledges,
“The results from this initial test support our approach to recycling blades, adding value, and challenging traditional waste disposal methods. Our goal is to reintroduce parts of the recycled material into the manufacturing of new wind turbines.”
As Europe moves towards a landfill ban, initiatives like this test are important steps toward creating circular economic opportunities that could be replicated globally.
“To advance turbine blade recycling, we need industry collaboration across all recycling methods. Not every blade can be repurposed into bridges or playgrounds, although straight repurposing is the ideal, we need to tackle the growing waste challenge together,”
– concludes Hanna Karlsson.
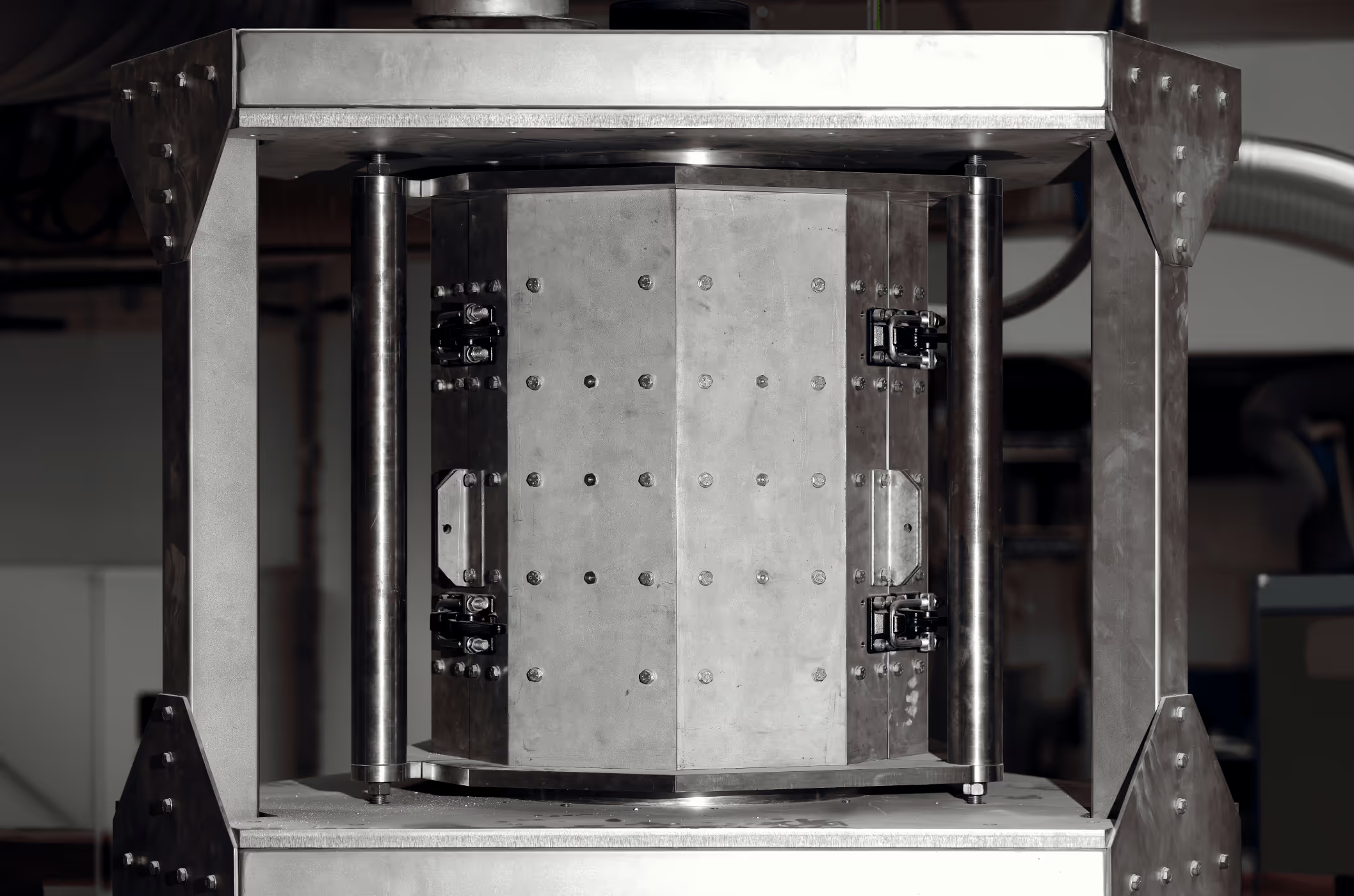
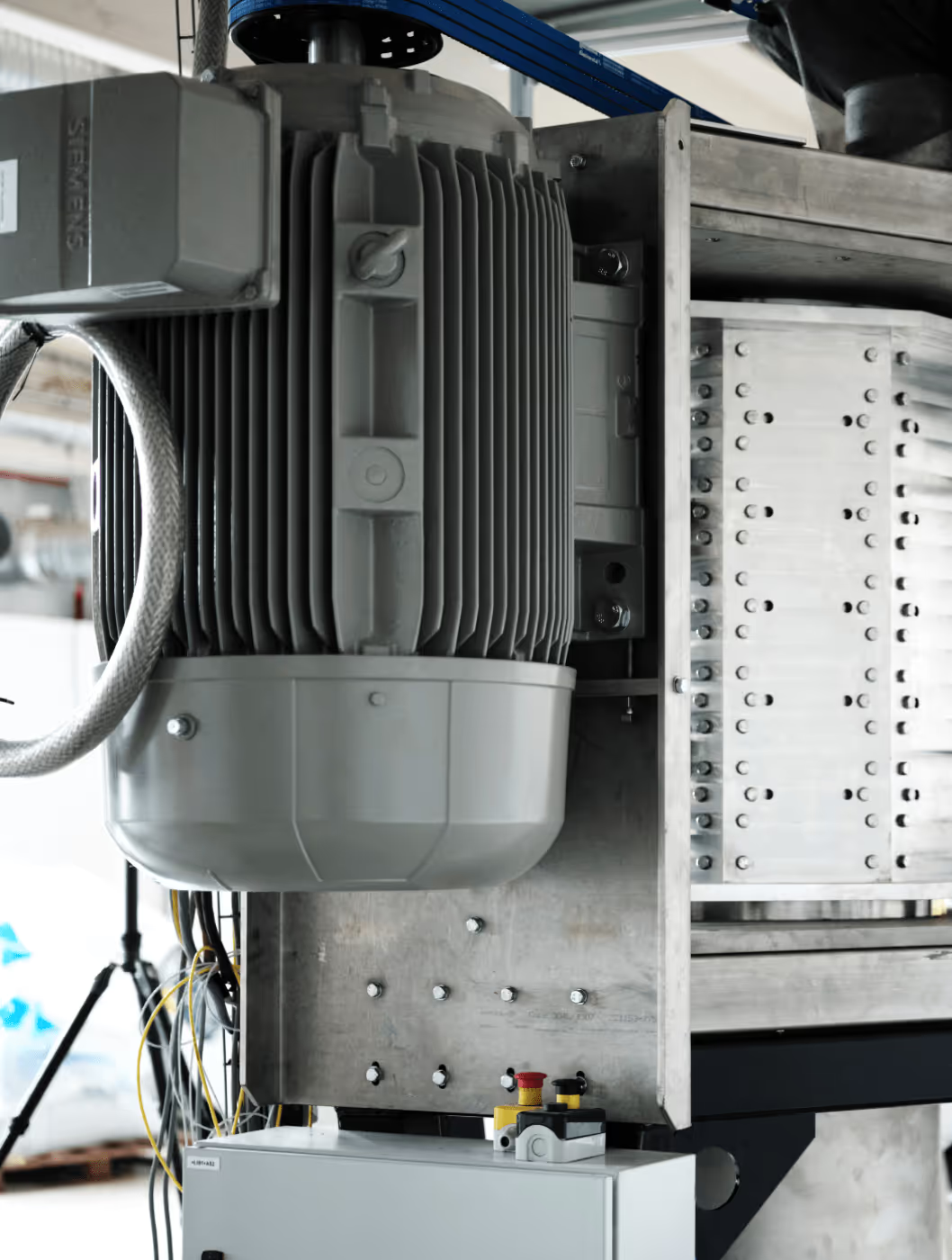
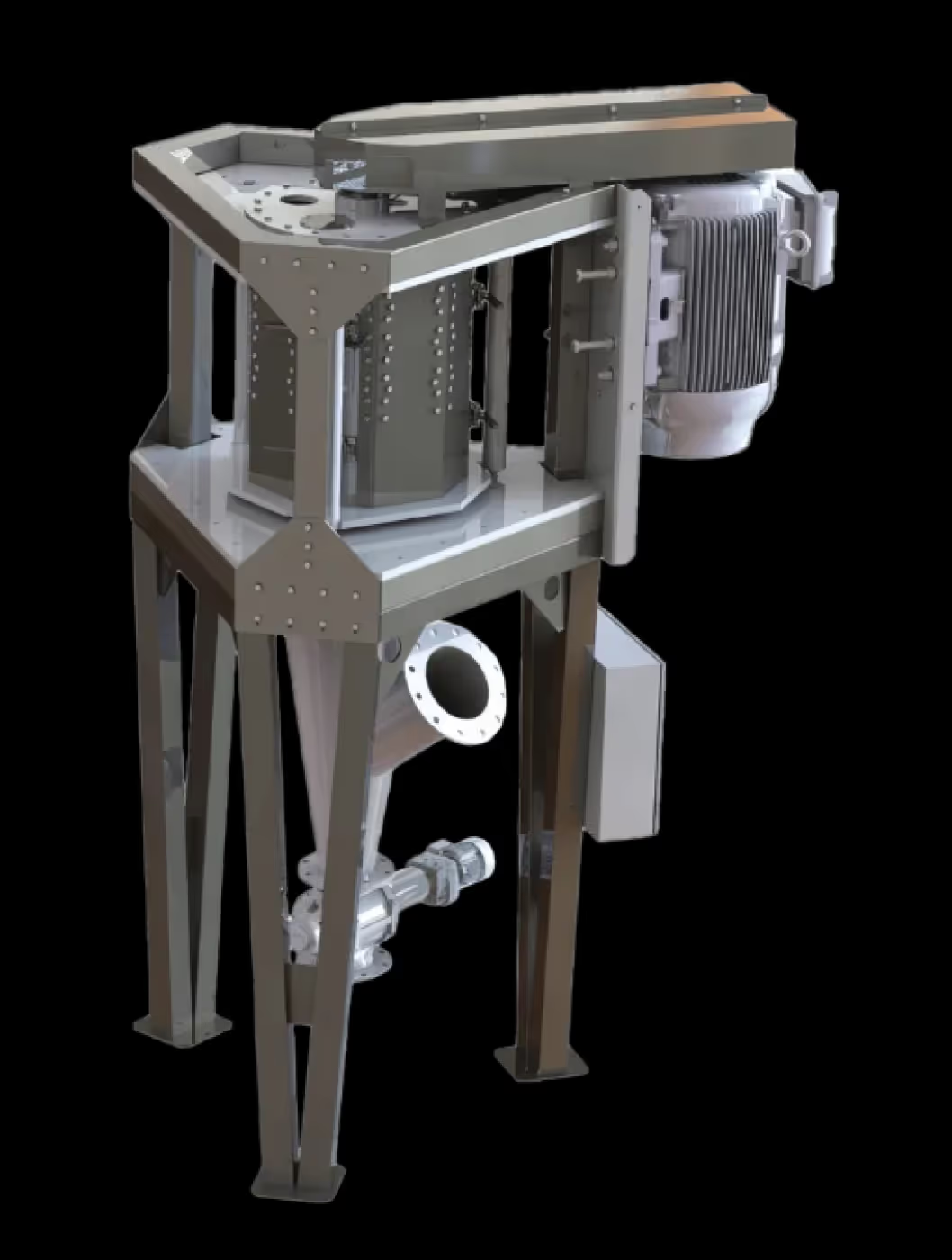
Our story
Lorem ipsum dolor sit amet consectetur. Et euismod est pellentesque id. Pellentesque vitae aliquet mauris ut sed est. Enim mi iaculis nisl viverra nulla risus. Tortor pulvinar pharetra ullamcorper condimentum nisi adipiscing mauris vitae in.
Morbi cursus cras vestibulum donec senectus enim massa odio purus. Mauris tempus enim donec vitae. Sed sit enim eget vel semper. Faucibus etiam lectus morbi magna nisl elit non. Euismod malesuada fames amet vel diam diam. Dui pretium varius quisque morbi maecenas.
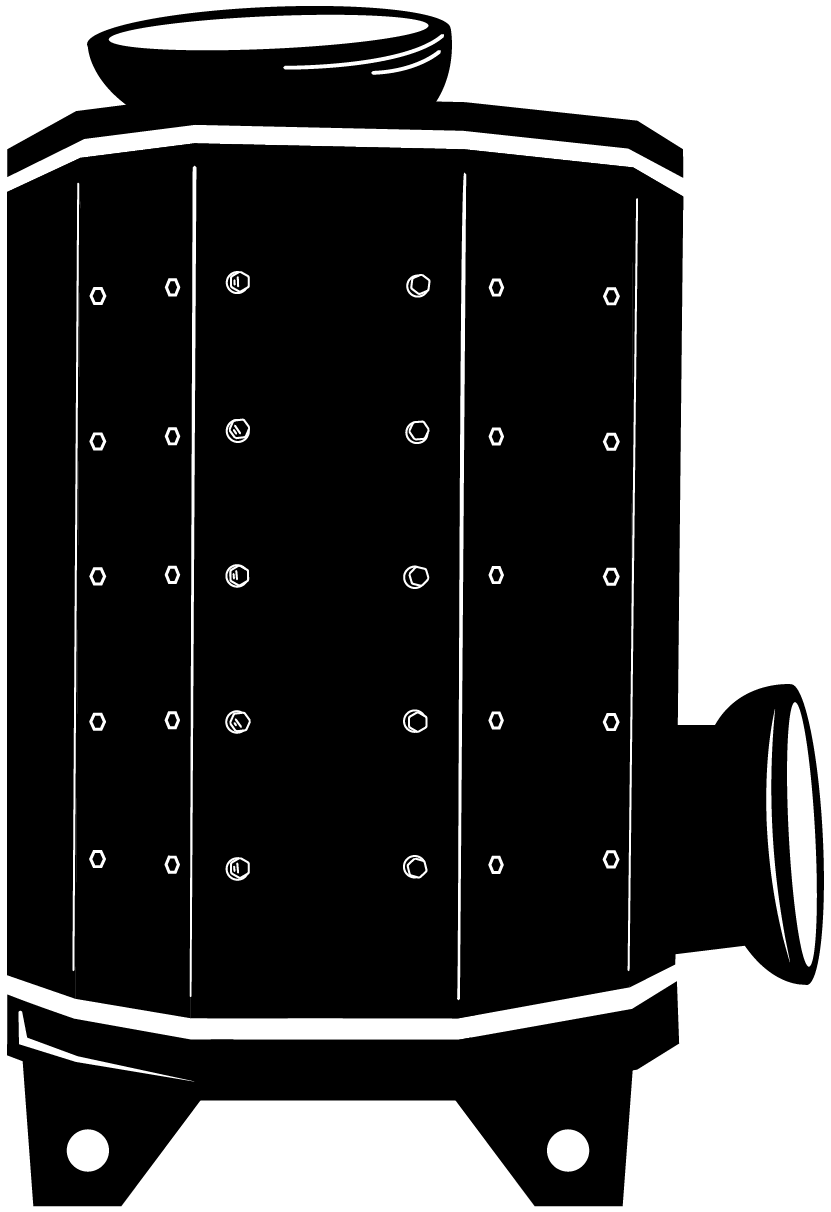