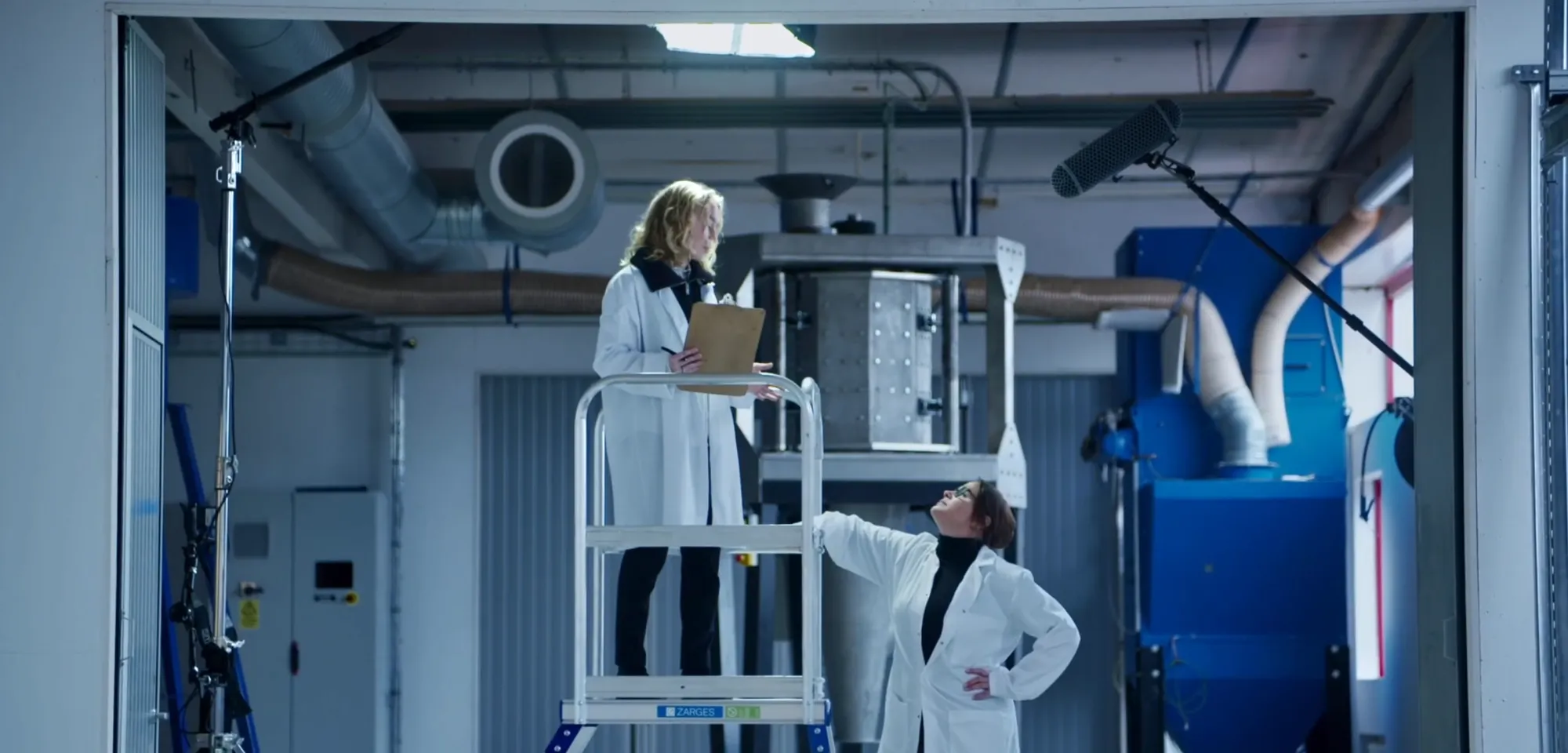
The Librixer Technology
With the Librixer technology it is possible to mechanically produce vegan protein, liberate metals from rocks, recycle glass fiber from wind turbines or reuse cotton fibers from textiles.
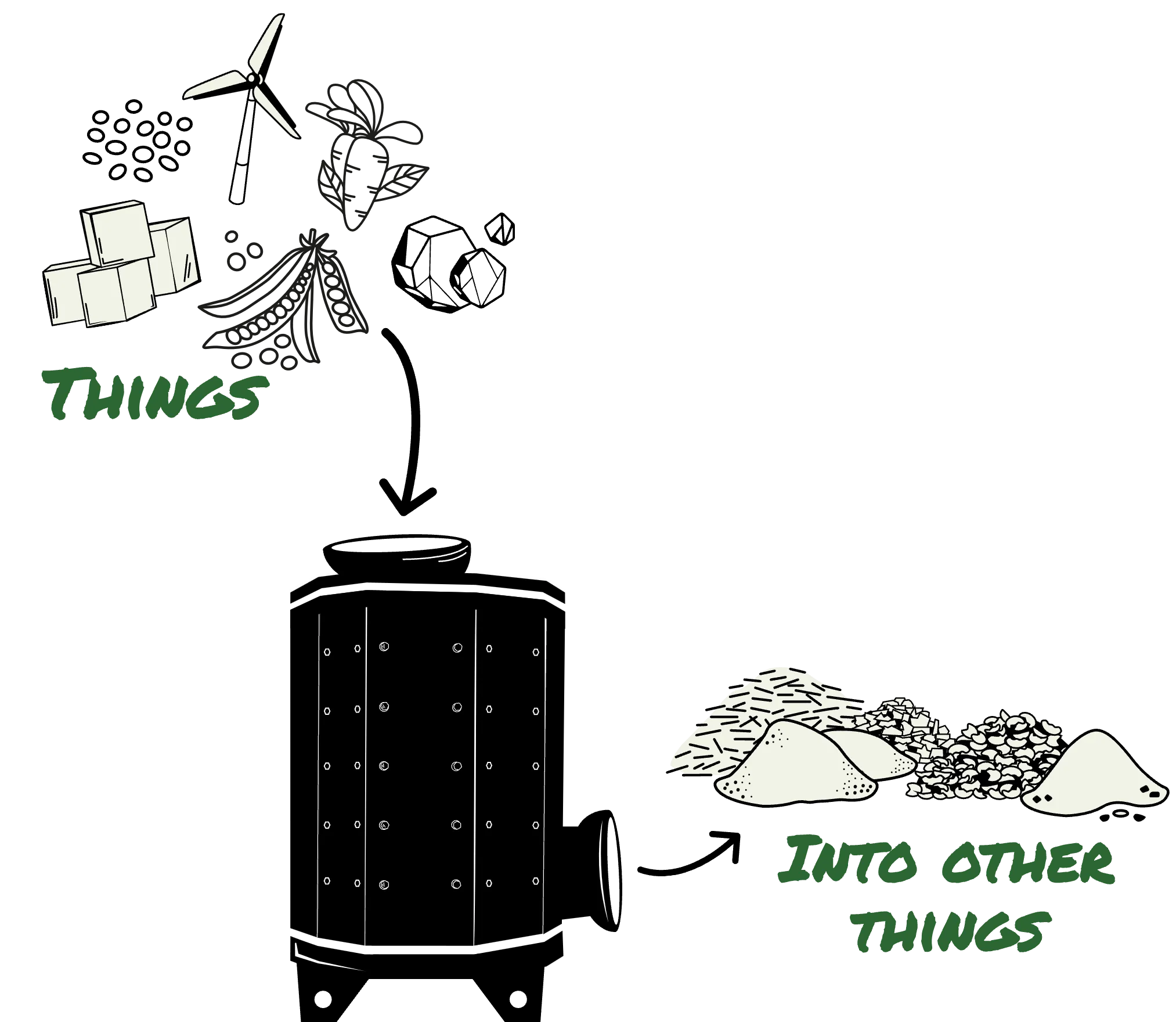
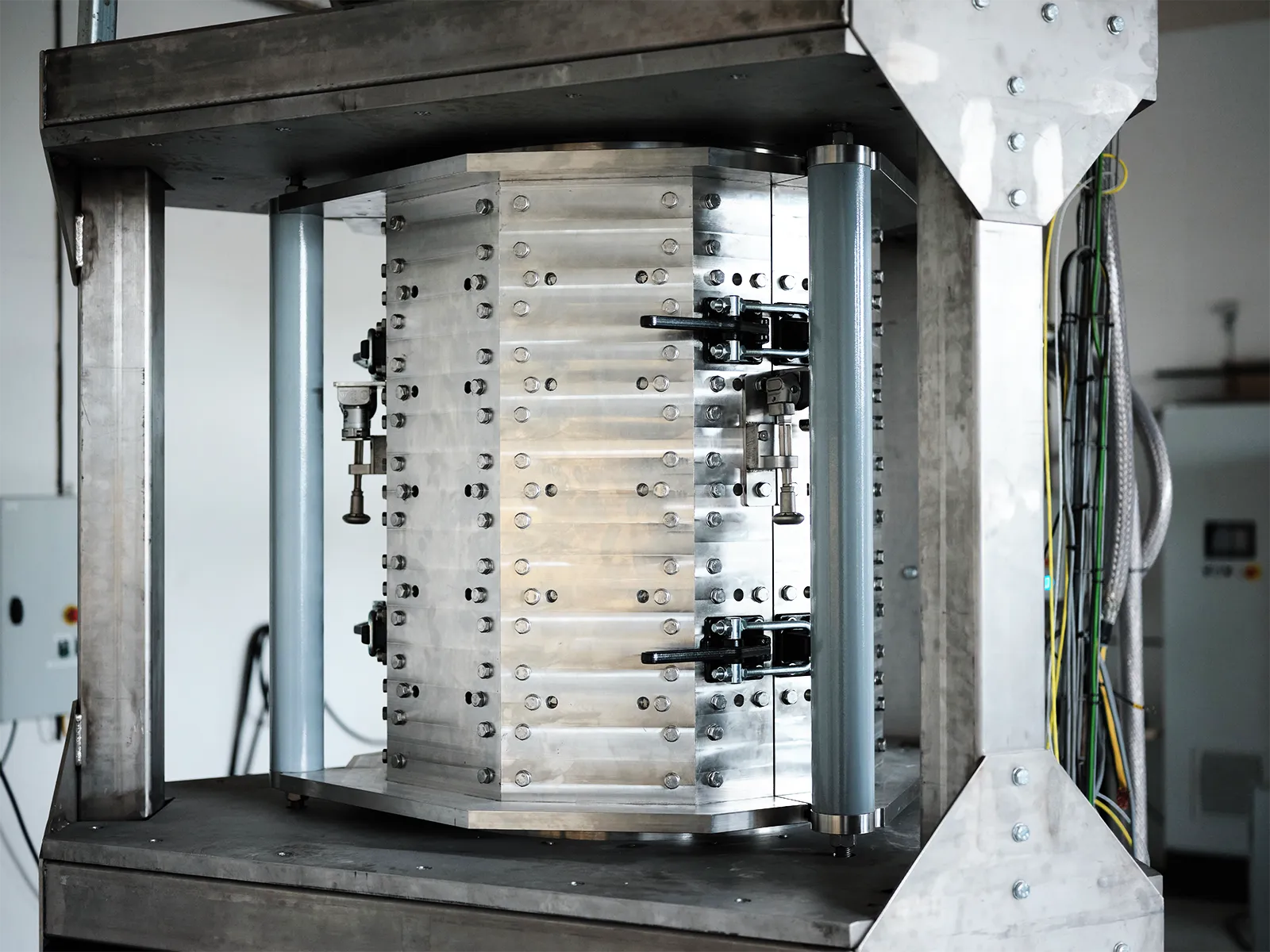
The Librixer Liberator
With the Librixer Liberator it is possible to mechanically produce vegan protein, liberate metals from rocks, recycle glass fiber from wind turbines or re-use cotton fibers from textiles.
- A dry, fast and energy efficient material comminution process.
- Makes the food production process more sustainable and efficient.
- Liberates protein and starch from legumes.
- Utilizes high frequency physics simultaneously to liberate and micronize materials.
- Enabling different materials to be purposefully both used and reused.
- You could call it magic – we call it a lean, clean anti-greenwashing machine.
Datasheets
Click the buttons below to alternate between our two machines
Librixer Micronizer
Process type
Continuous
Operating principle
High frequency, oscillating forces and random particle collisions
Operating speed
Up to 4000 rpm
Machine steel
SS-1.4301/1.4404
Surface finish
Standard Stainless Steel, Food grade Ra = 1.2 or Carbon Steel
Drive options
Top drive / Side drive with belt
Rotor assembly
6 vertical process chambers
Machine Options
With or without cooling
Weight
>3200 kg* (*depends on model)
Height (machine only)
3450 mm (Direct drive) / 2580 mm (Belt drive)
Footprint
1600x1500 mm (Direct drive) / 1600x1800 mm (Belt drive)
Floor distance outfeed pipe
265 mm (to center Ø200 mm pipe)
Electrical power
3×400 VAC (EEC), 90 kW motor
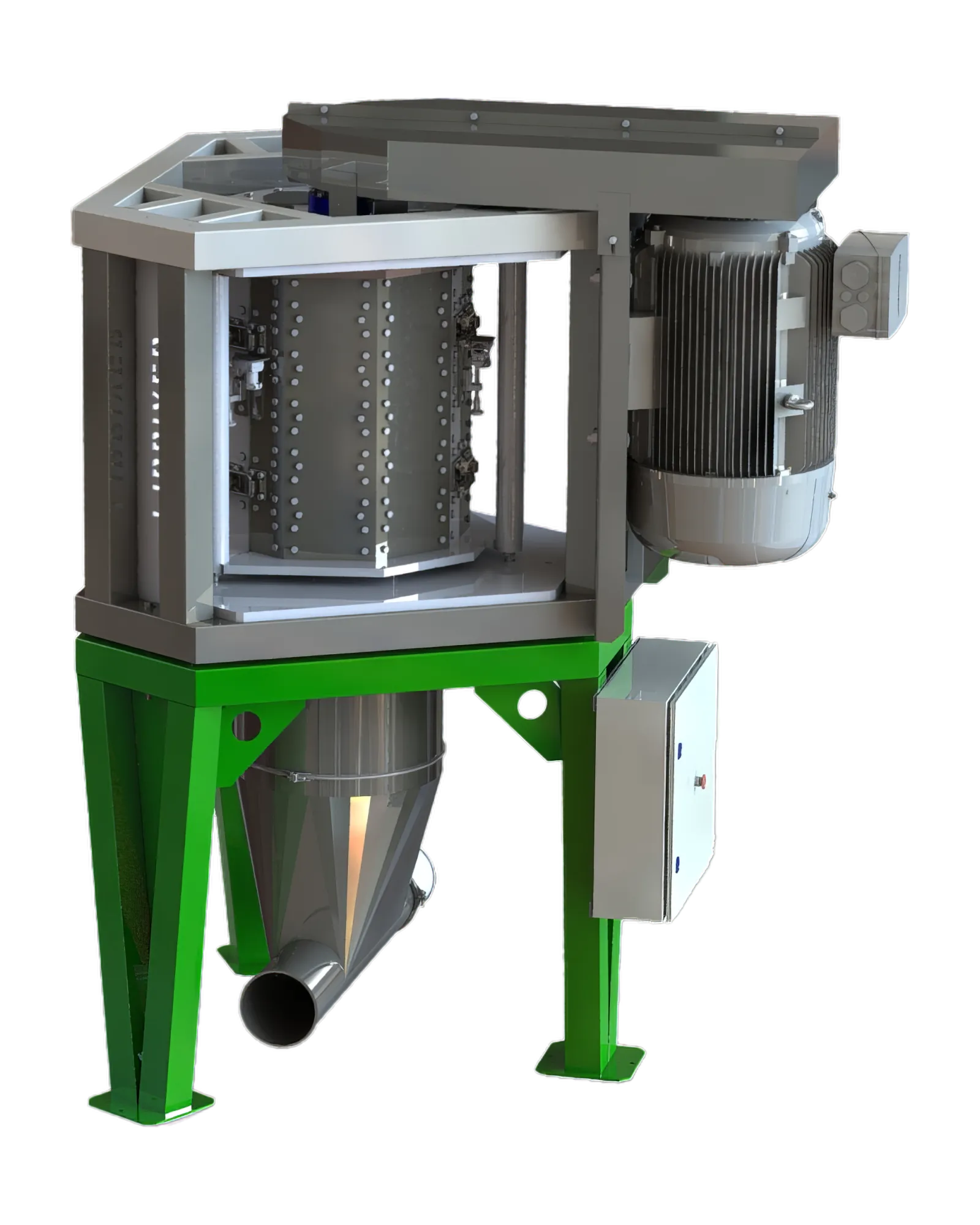
Librixer Fractionator
Process type
Continuous
Operating principle
High frequency, oscillating forces and random particle collisions
Operating speed
Up to 3000 rpm
Machine steel
SS-1.4301/1.4404
Surface finish
Standard Stainless Steel, Food grade Ra = 1.2 or Carbon Steel
Drive options
Top drive / Side drive with belt
Rotor assembly
4 vertical process chambers
Machine Options
With or without cooling
Weight
>3200 kg* (*depends on model)
Height (machine only)
3450 mm (Direct drive) / 2580 mm (Belt drive)
Footprint
1600x1500 mm (Direct drive) / 1600x1800 mm (Belt drive)
Floor distance outfeed pipe
265 mm (to center Ø200 mm pipe)
Electrical power
3×400 VAC (EEC), 75 kW motor
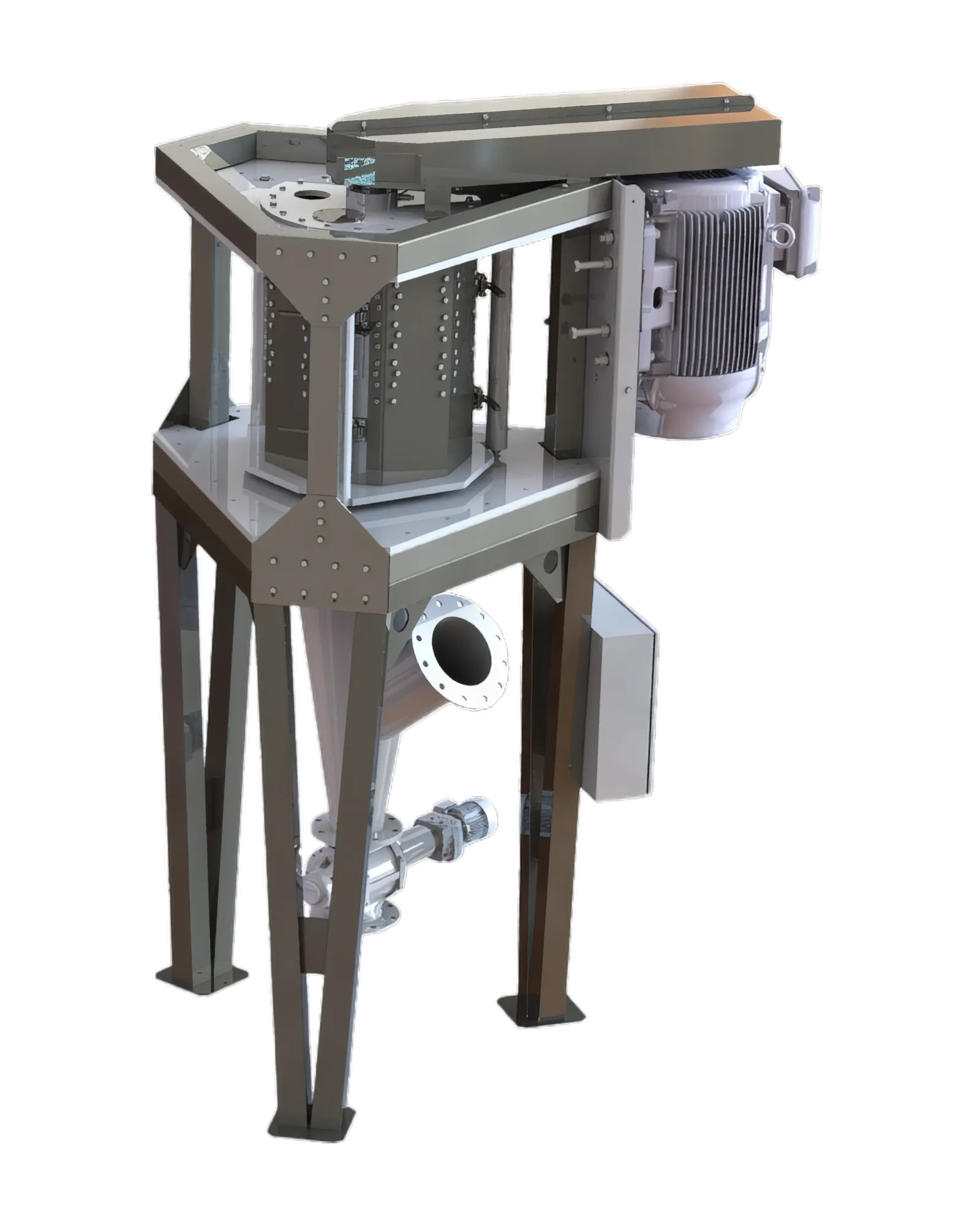
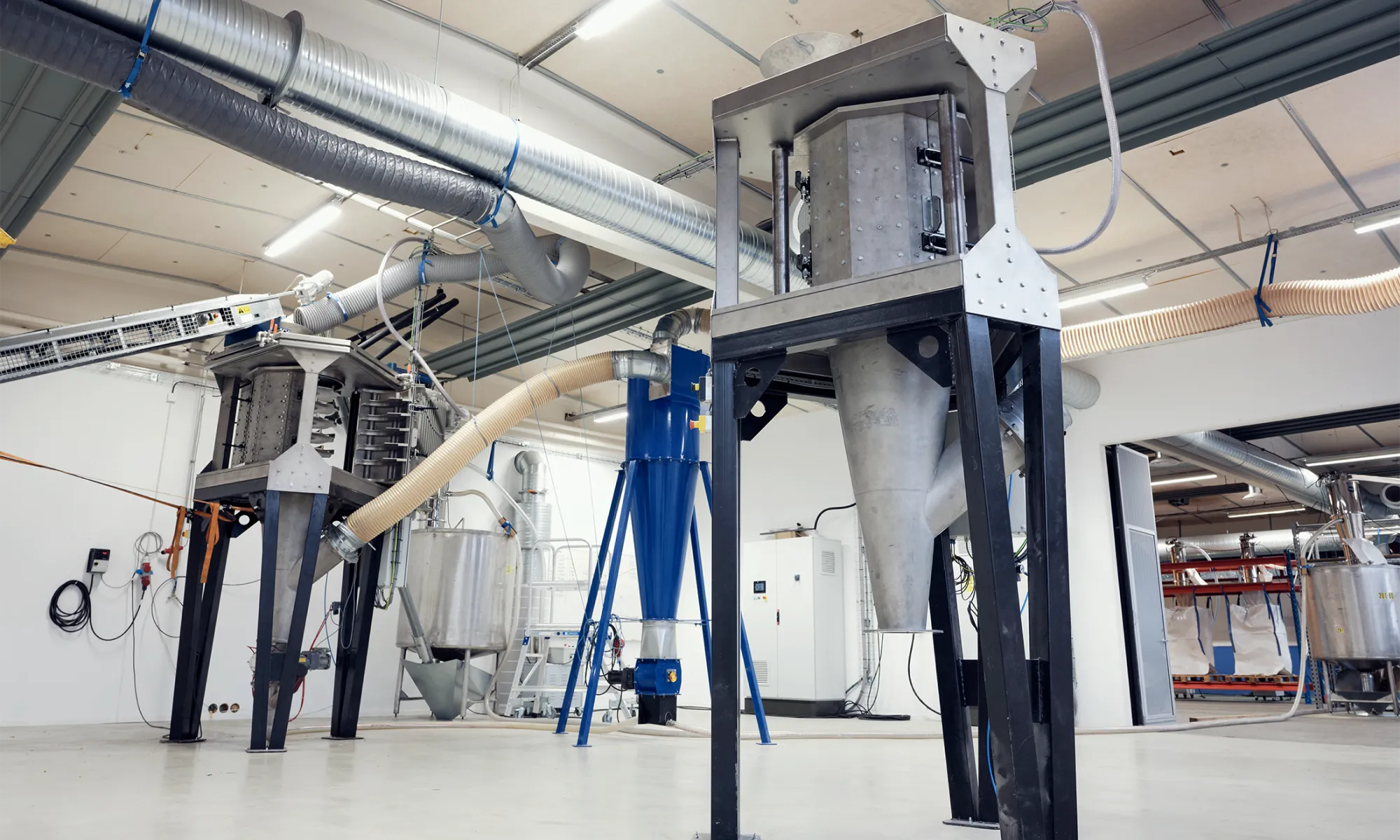
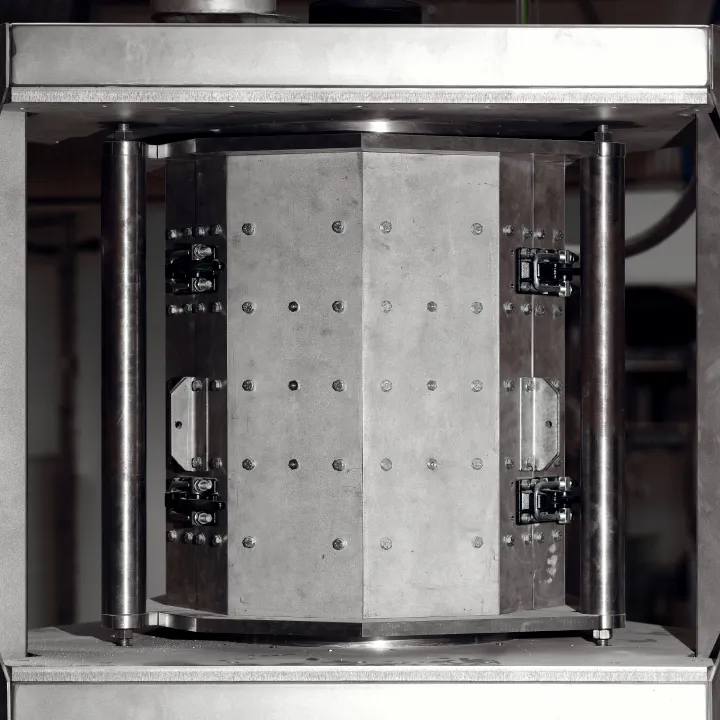
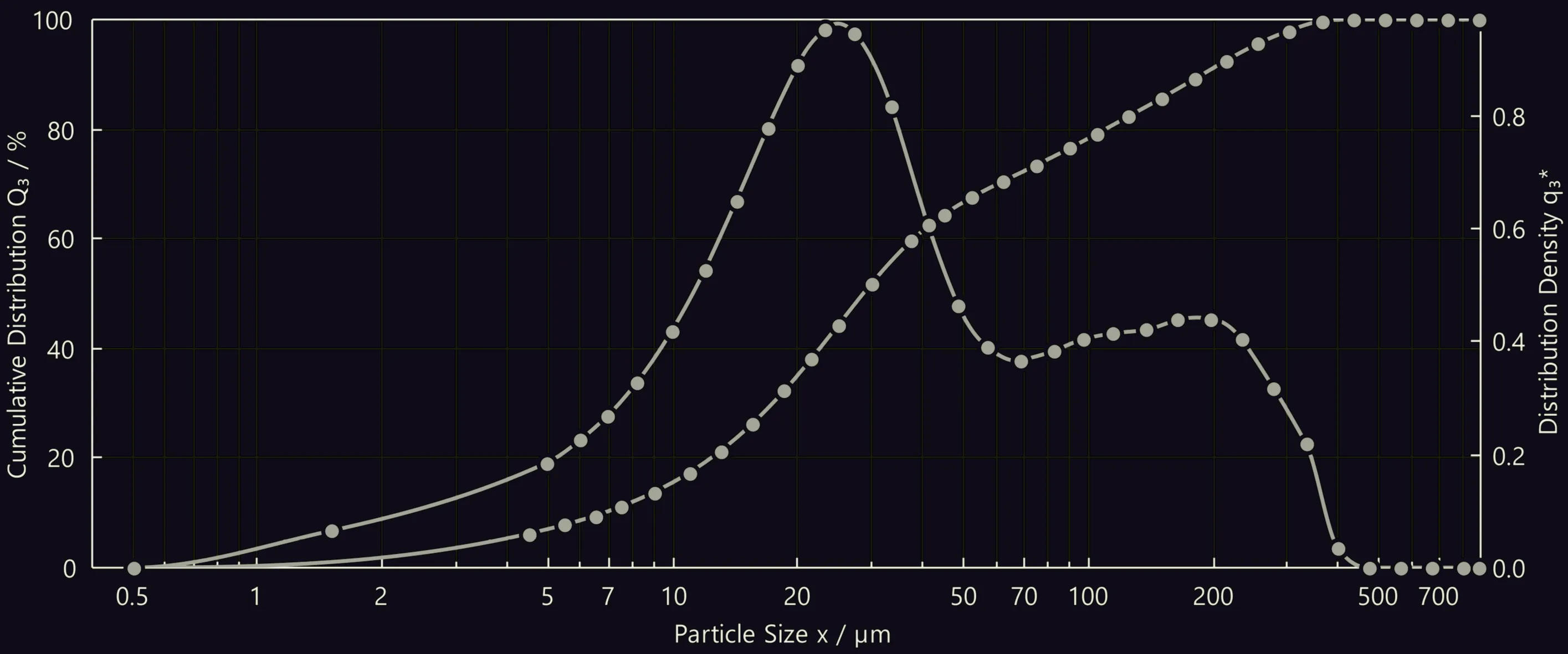
Bi-modal PSD diagram for oats
Traditional grinding techniques tend to normally result in a bell-shaped distribution curve. Our technology can, through release along natural boundaries, produce humped curves – which in turn facilitate mechanical sorting of composites where the different parts have different mechanical characteristics.
The diagram shows liberated, micronized and de-hulled oat kernels, where the pericarp's more flexible fiber structure commonly results in larger particles compared to the rest of the seed.
Example process
Where the Liberator fits into a general food process

Learn more about the Liberator in the context of food processing
Example of general food process
Lorem ipsum dolor sit amet, consectetur adipiscing elit.